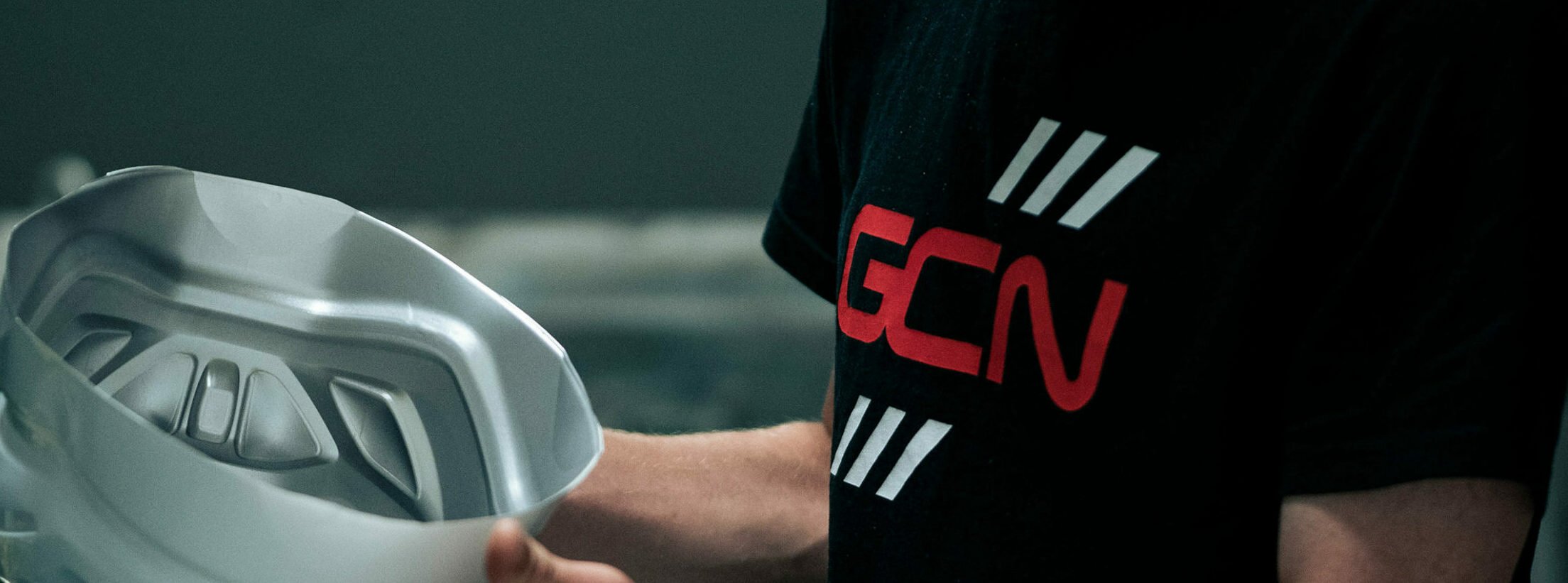
Behind the scenes
GCN visit MET Helmets HQ
📦 UPDATE ON SHIPMENTS & DELIVERY 📦
We inform you that for internal logistic reasons, orders placed from Friday afternoon 9th to Monday 12th May will be processed from Tuesday 13th May.
SUMMER BREAK
Thank you for visiting.
The MET staff is taking a well-deserved break, and shipments will resume starting August 20th.
Happy riding!
🚴♂️ TIME TO RECOVER AND RECHARGE! 🎄
We're taking some time off to recover, refocus, and get ready to ride at our best in the new year.
Orders will still be processed, but shipments will hit the road again starting January 7th.
Thank you for your patience, and we wish you a holiday season full of adventure ⛰️🌍